Houston, TX |
Thought of the Day
Fieldlink™ + Enbase™: Automating Field Workflows
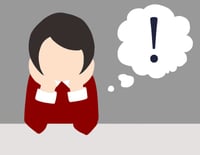
For compressor technicians, it is critical they know as soon as possible when one of their assigned units goes down. If the unit is monitored by an Enbase Hub, the tech can get a text message immediately upon their unit shutting down. The text message can include a link to Fieldlink where the tech can enter any key data like root cause and resolution details. This enables the technician to quickly fill in any details while they are fresh, perhaps even while they are still onsite, removing the need to type of a lengthy report later or to provide the information for someone else to log. This accurate, consistent and immediate data capture allows for better reporting and continuous improvement.
A service technician, operator or pumper may be more efficient and make better decisions with the right data at hand when performing a job… they can click a button to view the tag summary on their asset directly from Fieldlink to view things like Suction Pressure, driver speed or flow… or for low- or no-connectivity situations, they might want to have the past seven days of key data from their Hub attached to their service job for easy reference to answer questions like, “Do any unexpected data trends indicate need for additional maintenance or inspection?”
An administrator of an asset can be more efficient if asset information flows seamlessly between Enbase and Fieldlink. Fieldlink can be defined as the one-stop data entry portal allowing any updates made to a tank or compressor in Fieldlink to flow to Enbase, keeping details, such as billing codes, assigned technician, vendor or company association, etc. in sync between the systems.
Whether your goal is increased efficiency or more effective maintenance, consider how Fieldlink™ and Enbase™ can work together to improve and automate your field workflows.