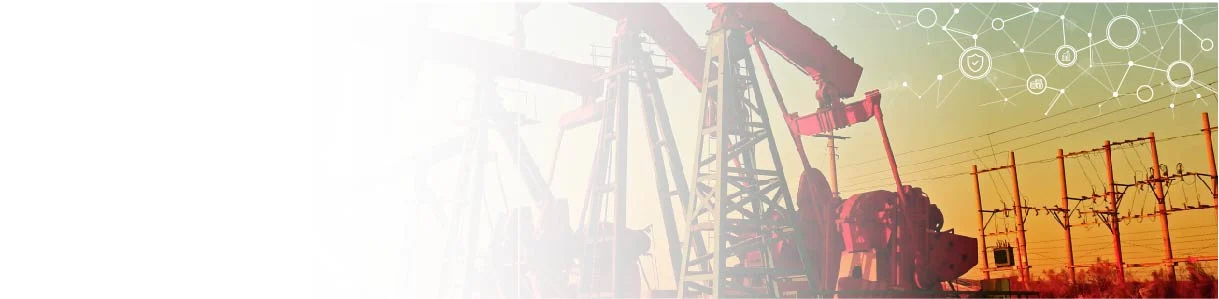
Reducing Lease Operating Expenses (LOE) for Oil And Gas Production
How Digitalization and Asset Optimization Reduce LOE
Why Current Oil & Gas Production Affects LOE
Oil and gas production encountered a world-historic challenge when Oil futures briefly traded in the negative numbers during April 2020. Many major and super major companies started merging for survival.
When oil and gas prices are low, the natural imperative for any oil company is to reduce both production and costs. Shrinking supply helps to offset demand, helping to return prices to "normal". Meanwhile, reducing LOE costs allows the company to manage staff efficiently and remain equipped so that it can return to a normal operating cadence when the market balances.
Case Study: LOE Reduction Challenges in the Permian Basin
In order to take a look at the challenges facing the industry at large, let’s look at a microcosm (albeit a large one) as an example. The Permian Basin, which is still one of the largest oil and gas producing regions in the world, is experiencing challenges such as aging and declining production.
Oil companies in the Permian Basin started to reduce their drilling operations (or having this necessity forced on them) while also attempting to decrease LOE. Their traditional methods included:
- Deferring maintenance expenses
- Divesting properties with higher costs
- Cutting production
- Furloughing personnel
The problem with the traditional approach is that the COVID-19 crisis was only the latest expression of a "new normal" in terms of lower oil production and gas prices at that time. Producers could not defer maintenance until production ramped up again. Not only would the pumps go offline, but the infrastructure could also fail in more-or-less permanent ways. There was perceived to be no way to resume production once prices returned to normal.
What’s more, producers could only cut production so much. Our natural gas clients experienced problems because running their compressors at reduced flow rates put them at risk of damaging their equipment. Oil producers faced similar risks. Running production equipment below normal operating thresholds can cause unexpected and undesirable behaviors—paradoxically increasing maintenance costs at the same time that decreasing LOE is most important.
In a nutshell, using IIoT can make traditional maintenance schedules a thing of the past. Operators can schedule less maintenance and leave equipment running for much longer without interruptions. They can then make more precise repairs and adjustments, resulting in shorter periods of planned downtime. This single aspect of IIoT can help oil and gas producers reduce their LOE and increase their revenue while growing their profits independently of the commodity market.
Powering Chemical Confidence.
Detechtion technology’s real-time resolution, data integration, and job management capabilities allow companies to manage and optimize chemical operations responsibly.
The LOE of Production
Maintenance is only a single (and very broad) aspect of a multidimensional picture when it comes to LOE. In addition to capital equipment maintenance, E&P companies must marshal the labor force to conduct maintenance and ongoing operations, dispose of saltwater byproduct, and manage chemicals used in the production process. As it stands, many if not most companies could stand to optimize at least one of these processes in order to reduce their LOE.
- Optimizing Compressors to Rescue Gas Wells
As a well grows older, the amount of oil or gas that it produces via free flow will begin to decline significantly. Using a wellhead compressor for gas lift lowers the density of the fluids inside the well, making the extraction of oil easier and unlocking years of extra production potential.
The primary challenge for operators is to ensure that the compressor generates enough production to exceed its ongoing operating costs, especially maintenance, which can become the largest expense.
One way Producers can reduce LOE is to reduce routine maintenance and inspection trips to the compressor itself by instrumenting the compressor and using sensor reading to determine whether the machine can operate safely. Doing so allows producers to remotely restart their compressors without arranging an inspection tour, dramatically decreasing planned downtime and increasing production.
- Environmentally Compliant Disposal
The same frangible rocks that contain oil and natural gas also contain saltwater, which is then produced as a byproduct of drilling. On an offshore oil rig, disposing of this byproduct is usually as simple as letting it flow back into the sea. Inland oil wells such as those found in the Permian Basin will experience more complex disposal challenges.
On land, saltwater is an environmental hazard that can poison local ecosystems, and its treatment requires careful consideration. The most common decision is to drill a second dry well alongside the first, pump saltwater into it, and then cap the well with non-porous rock.
Coordinating the disposal of wastewater can be difficult in this manner. The material should be pumped as soon as possible, and every day that it remains aboveground represents an additional storage cost. In order to minimize LOE related to saltwater, producers should expedite disposal using the optimal combination of personnel and equipment. If an operator mismatches disposal capacity with its need to dispose of saltwater, then the operator risks paying unnecessary overhead.
- Saltwater Separation and Pipeline Maintenance via Chemical Mechanisms
Chemical treatment is a foundational step in the oil production process. Separating crude oil into its various grades is an intense process that doesn’t start at the refinery, but rather at the well itself. Chemical additives can be used to: help separate oil from saltwater; thin out paraffin and asphalt to prevent blockages in the well and pipelines; clean emulsions on the bottom of tanks; and prevent wells from becoming shut-in. Purchasing and deploying these chemicals can represent a major component of a company’s LOE.
Once again, there are several variables at play and questions one should ask when determining whether a production company is spending wisely on their chemical management program. For instance, are batch (or “truck”) treatments occurring at the correct frequency and intervals? Are the dosages of chemicals injected for continuous chemical treatments correct? Under-dosing chemicals has the potential to expose operators to expensive equipment damage or even well shut-ins that result in both lost production and costly well workovers. On the other hand, overdosing results in wasting chemicals and money.
By implementing IIoT sensors within the production environment, the company could achieve an empirical understanding and adjust injection or dosage rates as necessary. In addition, producers can optimize their use of chemicals with flexible automation, allowing them to stop chemically treating shut-in wells or automatically change their use of chemicals based on fluctuating weather conditions.
- Optimizing the Labor Pool for Efficient Operations
Labor, like maintenance, is a fairly broad aspect of a multidimensional LOE picture. A traditional oil well utilizes labor during almost every stage in the production process, but out of necessity, this is beginning to change.
During the early part of the 2010s, the oil industry went through what’s known as The Great Crew Change. A huge portion of the workforce retired—taking their institutional knowledge with them—and leaving much of the remaining personnel composed of under-35s. Additionally, low oil prices have depressed hiring budgets, which means that there isn’t much new talent entering the field.
Lease operating expenses surge when this newly shrunken workforce is deployed ineffectively. When equipped with mobility options and industry 4.0 applications, each crew member can cover a large area, addressing problems remotely and preemptively. Companies can always ensure that their crews are equipped to do the job they’re assigned, minimizing repeated trips, and potentially the crew's safety. In addition, they can ensure that their crews prioritize the most important tasks—instead of running down the same rote checklist every time they visit a production site.
To mitigate the LOE, oil companies need a solution that does more than simply reduce maintenance costs. They need an expansive digital toolkit that helps them optimize their operational expenses over every aspect of the production process.
How Digitization and Asset Optimization Reduces Oil and Gas LOE
When it comes to effectively managing equipment, chemicals, personnel and data, oil and gas producers have a long way to go. Although many companies have begun to implement automation, few have holistic solutions that cover more than just their machinery. Here at Detechtion Technologies, we offer solutions that cover the full spectrum of challenges that producers face.
- Optimize Natural Gas Compression Programs
All three of Detechtion’s flagship products help producers get the most out of their compressor technology:
- Enbase IIoT delivers timely and accurate visibility to their compressors’ status, including alerting on unplanned shutdowns and an understanding of true asset availability. With this insight and knowledge, producers can save costs by pushing preventive maintenance schedules based on actual run hours. Additionally, they can reduce downtime and mean time to repair by dispatching the right person with the right skills and the right tools.
- Enalysis Asset Performance Management (APM) identifies predictive maintenance opportunities to identify (and repair) problems before they occur, reducing unplanned shutdowns and associated downtime, lost production, and expensive repair costs. Operators can save additional costs by using this insight to further extend customary PM schedules when needed.
- Enalysis also identifies production optimization opportunities to increase throughput or reduce fuel/power consumption – or sometimes both! And these opportunities are ranked for the producer with predictive maintenance opportunities based on associated cashflow at risk to ensure that the operator is sending field workers where they can make the biggest impact on the business.
- Fieldlink Mobile Oilfield Management allows field workers to collect additional asset data that is not instrumented (no sensors) from any device—phone, tablet or computer. Fieldlink also empowers operators to dispatch field workers electronically for proactive activities like preventive or predictive maintenance and optimization opportunities; or for reactive needs like unplanned shutdowns thereby improving transparency, accuracy and efficiency. If an asset needs attention, Fieldlink will surface that information to the appropriate field-workers and personnel.
- Run Efficient Chemical Management Programs
Effectively managing an oilfield production chemical program requires the operator to manage both their batch and continuous programs across multiple chemical providers. Your workforce, including your chemical providers, should use a streamlined and holistic solution that that covers both the batch and continuous treatments, as well as other associated chemical activities, including lab analysis.
By using Enbase to monitor continuous chemical injection programs and Fieldlink to digitize its associated activities and workflows, a producer can:
-
- Reduce downtime avoiding lost production and prevent well workovers
- Avoid expensive equipment damage
- Ensure appropriate dosing which saves on chemical spend while assuring production flow
- Improve transparency, accuracy (including invoicing integrity) and efficiency by consistently collecting performance data across multiple chemical suppliers/vendors
- Bring Digital Transformation to the Oilfield with Fieldlink
When different parts of an organization are unable to freely share information with each other, production suffers. Communication turns into a game of telephone—a sheet of paper on a clipboard turns into a spreadsheet which turns into an email. Every jump between medium is an opportunity to lose or misinterpret information.
Fieldlink solves this problem by delivering a single platform and user interface for all oilfield activities. By digitizing previously paper-only forms and automating previously manual and fragmented business processes, Fieldlink provides the business full transparency and auditability of work performed by both employees and third-party service providers. Operators benefit from this capability by having proof of service for outsourced oilfield activities, while ensuring invoicing accuracy and integrity.
About Detechtion Technologies
- Improving production
- Enabling manage-by-exception processes,
- Avoiding unnecessary equipment shut down
- Gathering data cost-effectively
- Preventing costly equipment repairs
- Streamlining ticketing and other supplier processes
There are millions of oilfield assets and many are left unmonitored, and in need of optimization to deliver lower operating costs while maintaining top production. Lowering your LOE, operating more efficiently, and maintaining safety and regulatory compliance requires a new, digital approach.
Industry analysts report that asset optimization is being rapidly accelerated through the adoption of IIoT.
Our experience with producers confirms two things: First, data acquisition from remote assets and collecting manual data from field workers is an acute problem in the oilfield. Secondly, the benefits from digital technologies can drive meaningful improvements to operations.
Detechtion is a leader in asset optimization. We deliver a unique product suite of Asset Performance Management (APM), Industrial Internet of Things (IIoT) and Mobile Oilfield Management solutions.
Each product is designed to improve oilfield operations. Used together, they enable best-in-class operations, leading to lower operating costs and improved production.
We know our customers’ business needs because we've maintained focus exclusively on Upstream and Midstream Oil and Gas through the years.
Detechtion delivers the digital transformation and optimization of natural gas compression, oilfield chemicals, and other production operations, to save our customers millions of dollars each year.
If you feel as though the economic climate has put a ceiling on your ability to generate revenue in production, reducing your LOE could help greatly.
Schedule a Discovery Call today to discuss how we can help!
Seeing is Believing.
Schedule a demonstration with our experts and see how we can help your fleet gain visibility and control.