Houston, TX |
Representative Win
Increased Throughput – Maximizing Power Usage
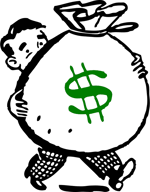
Proposed
Optimize the client’s compressor station to maximize production and increase overall utilization.
Background
A compressor station composed of two identical reciprocating compressors was commissioned in a high activity field aimed to accommodate high flow rates and variable conditions. Cylinder actions were setup as single-acting to accommodate the variable conditions resulting in high uptime, and swinging gas flow rates. The subsequent year, activity in the field slowed and the rates/pressures steadied. With the steadied pressures and slowly declining gas rates, the two compressors became ideal candidates for optimization as identified through Enalysis™’ Cash Flow at Risk and Incremental Production calculations.
In an on-going effort to improve on and meet production targets, the gas producer opted to pursue the potential for increased production through compressor optimization.
Optimization Methodology
For a reciprocating compressor to be fully optimized for maximum throughput, either or both of the cylinder capacity utilization and the horsepower utilization should be 100%. Through the use of individual compressor performance curves, such as the one below, and a Detechtion Technologies’ Start-up Package of high and low pressure set points, detailed in this edition’s Tech-Tip, compressor units can be evaluated for opportunities to:
- Increase running speed
- Adjust cylinder action
- Reduce added cylinder clearance
- Optimize suction pressure
- Decrease recycle set point
Thus resulting in increased utilization and maximum throughput.
Outcome
After a detailed review of the current compressor station operating parameters through Detechtion Technologies’ Enalysis™ system, a new configuration with new high and low pressure set points were presented to the gas producer. With the new configuration, the compressors were capable of flowing more gas at much lower suction pressures than the current plant inlet pressure.
The new pressure set points were programmed into each panel to protect the compressors, the stage 1 cylinders were changed to double acting from single acting, the pockets were adjusted to 1.75” and the suction set-point decreased by 23 psig to pull harder on the field and increase production.
The changes resulted in approximately 4.6 mmscfd of additional throughput for the station as the field production was stimulated by the lower suction pressure. For the time frame that was closely observed, the units sustained an average production increase of 4.6 mmscfd over the following 30 days, equating to an immediate $414,000 in revenue increase for the time frame observed, assuming $3.00/mscf that, when annualized, resulted in $5,037,000 in increased revenue!
Compressor Configurations | Power Usage | Suction Pressure | Discharge Pressure | Station Throughput | |
---|---|---|---|---|---|
Before | SAHE0”,SAHE0”//DA0”//DA0” | 74% | 75psig | 750psig | 11.0mmscfd |
After | DA1.75”,DA1.75”//DA0”//DA0” | 96% | 52psig | 750psig | 15.6mmscfd |
Change | +22% | -23psig | 0psig | +4.6mmscfd |